Safety valves can be divided into four categories, namely, hammer type safety valves, lever type safety valves, spring type safety valves, and pilot type safety valves. So what are the requirements for its use? Follow me today to learn more about it.
A, the classification of safety valves
1, the hammer type safety valve: it is a heavy hammer for the load, directly applied to the valve flap. This structural form has many shortcomings, and is rarely used.
2, the lever hammer safety valve: the hammer is loaded on the valve flap through the lever, the load does not change with the opening height, but more sensitive to vibration, and poor return to the seat performance. It consists of valve body, valve cover, valve stem, guide fork (to limit the up and down movement of the lever), lever and hammer (to regulate the role of pressure on the valve flap), prismatic support and force seat (to improve the role of sensitive action), the top seat (to determine the role of the stem position), throttle ring (the same role as the recoil disc), support head screws and set screws (to fix the role of the hammer position) and other parts. Usually used for lower pressure systems.
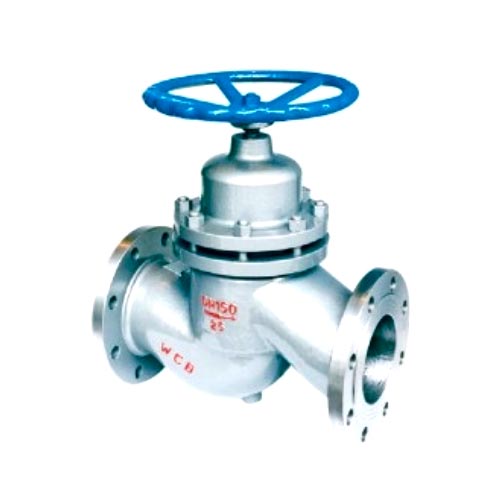
3, spring type safety valve: through the role of the spring force on the valve flap to control the opening and closing of the valve flap. It has a compact structure, small size, light weight, reliable opening and closing action, insensitive to vibration and other advantages; its disadvantage is that the load acting on the valve flap with the opening height and change. The performance requirements of the spring are very strict and difficult to manufacture. It consists of the following main parts.
① Valve body and valve cover. The valve body inlet channel and the discharge port channel is 90 ° angle, similar to the angle shut-off valve. Spring safety valve has two types of closed and unclosed. The outlet channel of the closed safety valve is connected to the discharge pipe, and the medium in the container or equipment is discharged to the intended place.
Unclosed safety valves do not have a discharge line, and the medium is discharged directly into the surrounding atmosphere, which is suitable for non-polluting media. The valve cover is a cylinder, containing the stem, spring and other parts, and is connected to the valve body with flange bolts.
② Valve flap and valve seat. According to the opening height of the valve flap, the safety valve can be divided into two kinds of micro-opening and full revelation. Micro-opening safety valve, mainly used in liquid media, the valve opening height is only 1/40 to 1/20 of the seat throat diameter, the valve and seat structure is similar to the globe valve, the seat is placed on the adjustment ring. Fully open safety valve, see Figure 2-67, mainly used for gas or steam occasions. The opening height of the valve is equal to or greater than 1/4 of the throat diameter of the valve seat.
③Dispersion spring and upper and lower spring seats. The spring is fixed between the upper and lower spring seats. Spring force through the lower spring seat and the valve stem act on the valve flap, the upper spring seat is positioned by the adjusting bolt, twist the adjusting bolt can adjust the spring force, so as to control the opening pressure of the safety valve.
④Adjustment ring. It is to adjust the opening and closing pressure difference parts.
⑤ Backlash disc. Connected with the valve flap, it plays the role of changing the flow direction of the medium, increase the opening height, used in the fully open safety valve.
In addition, from the external structure, it can also be divided into with and without wrench, with and without bellows, with and without heat sink, etc. Safety valve with bellows is suitable for corrosive media or back pressure fluctuations; safety valve with wrench can be manually operated in case of emergency to relieve pressure; safety valve with heat sink is suitable for media temperature greater than 300C.
4, pilot operated safety valve: it consists of a main valve and a subvalve, the lower part is called the main valve, the upper part is called the subvalve, the role of the subvalve to drive the action of the main valve safety valve, when the medium pressure exceeds the rated value, it compresses the subvalve spring, so that the subvalve flap rises, the subvalve opens. So the medium enters the top of the piston cylinder. As the area of the piston cylinder is larger than the area of the main valve flap, the pressure pushes the piston down, driving the main valve flap to move down to open, and the medium is discharged outward. When the medium pressure drops below the rated value, the secondary valve flap closes under the action of the secondary valve spring, and the main valve piston has no medium action, the piston springs back under the action of the spring, plus the pressure of the medium to close the main valve. The pilot operated safety valve is mainly used for large diameter and high pressure applications.