Neglecting track roller maintenance on an excavator can lead to various negative consequences, affecting both the performance of the machine and its overall longevity. Here are some potential consequences of neglecting track roller maintenance:
- Reduced Equipment Performance: When track rollers are not properly maintained, they can wear down, causing uneven wear on the tracks. This, in turn, can lead to reduced equipment performance, including slower speed, decreased maneuverability, and diminished digging and lifting capabilities.
- Increased Fuel Consumption: Worn or misaligned track rollers can create more friction, causing the excavator’s engine to work harder. This increased strain can result in higher fuel consumption and operational costs.
- Unscheduled Downtime: Neglected track rollers are more prone to sudden failures or breakdowns, leading to unscheduled downtime. This can disrupt construction or excavation projects, leading to delays and financial losses.
- Risk of Accidents: Damaged or worn track rollers can compromise the stability and safety of the excavator. This increases the risk of accidents, especially on uneven or sloping terrain.
- Higher Repair Costs: Delaying maintenance often leads to more extensive damage, resulting in higher repair costs. Replacing severely damaged track rollers can be more expensive than regular maintenance or timely replacement.
- Shortened Equipment Lifespan: Neglecting track roller maintenance can significantly reduce the overall lifespan of the excavator. This means that you may need to replace the machine sooner than expected, incurring a substantial capital expense.
- Damage to Other Components: Neglected track rollers can affect the entire undercarriage system, leading to damage to other components like the idlers, sprockets, and drive motors. This, in turn, increases the scope of required repairs and costs.
- Environmental Impact: Increased fuel consumption and potential oil leaks from damaged components can have an adverse environmental impact, contributing to pollution and environmental degradation.
- Reduced Resale Value: A poorly maintained excavator with neglected track rollers will have a lower resale value when you decide to sell or trade in the equipment.
- Safety Risks: The safety of the operator and those working around the excavator is compromised when maintenance is neglected. China roller excavator Sudden failures or accidents related to track roller issues can lead to injuries or fatalities.
To avoid these consequences, it’s crucial to adhere to a regular maintenance schedule and perform routine inspections to identify and address track roller issues promptly. Proper maintenance not only ensures the excavator’s longevity but also contributes to safe and efficient operation.
Can you describe the process of replacing or repairing track rollers on an excavator?
Replacing or repairing track rollers on an excavator is a complex process that should ideally be performed by trained technicians or professionals. Here is a general overview of the steps involved in the process:
Tools and Equipment: Before you start, gather the necessary tools and equipment, which may include wrenches, sockets, a jack, jack stands, a track press, and replacement track rollers.
1. Safety Precautions:
- Ensure the excavator is turned off and the engine is cooled down.
- Use proper safety gear, such as gloves, safety glasses, and protective clothing.
- Block the tracks to prevent accidental movement.
2. Lift the Excavator:
- Use a hydraulic jack and jack stands to lift the excavator safely off the ground, providing access to the undercarriage.
3. Remove the Damaged Track Roller:
- Locate the damaged track roller and remove any components that may be obstructing access to it, such as guards or covers.
- Loosen and remove the bolts securing the damaged track roller to the track frame.
- Carefully slide the damaged roller out of its position.
4. Inspect the Track Frame and Undercarriage:
- While the track roller is removed, inspect the track frame and undercarriage for signs of damage, wear, or misalignment.
5. Install the Replacement Track Roller:
- Position the new or refurbished track roller in place.
- Reattach and tighten the securing bolts to the manufacturer’s specified torque settings.
- Ensure that the roller is properly aligned and seated.
6. Lubrication and Adjustment:
- Grease the newly installed track roller according to the manufacturer’s recommendations.
- Check the tension of the track and adjust it as necessary. Proper track tension is crucial for even wear on the rollers and efficient operation.
7. Lower the Excavator:
- Carefully lower the excavator back to the ground using the hydraulic jack and remove the jack stands.
8. Test the Excavator:
- Start the excavator and test its operation, including track movement and stability, to ensure that the replaced track roller functions correctly.
9. Regular Maintenance:
- Implement a regular maintenance schedule to ensure that all track rollers and undercarriage components are inspected, lubricated, and maintained according to the manufacturer’s recommendations.
It’s important to note that the process may vary depending on the make and model of the excavator, and specific instructions should be followed from the manufacturer’s manual. Additionally, for more extensive repairs or if you are not experienced in heavy equipment maintenance, it’s advisable to consult with a qualified technician or service professional to ensure the work is done safely and effectively.
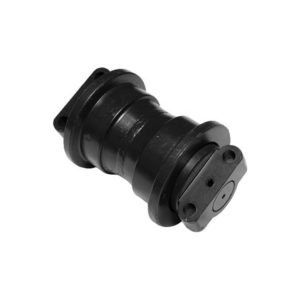