China is a leading producer of non-woven fabric machines, and there are many different types of machines used in the production of non-woven fabrics.
Here are five of the most common non-woven fabric machines manufactured in China:
Spunbond Non-woven Fabric Machine: This machine is used to produce spunbond non-woven fabrics, which are made by extruding molten polymer through spinnerets and then bonding the resulting fibers together using heat or pressure. Spunbond fabrics are commonly used in medical and hygiene products, as well as in geotextiles and other industrial applications.
Meltblown Non-woven Fabric Machine: Meltblown machines are used to produce meltblown non-woven fabrics, which are made by extruding ultra-fine polymer fibers onto a conveyor belt using high-pressure air. Meltblown fabrics are known for their high filtration efficiency and are commonly used in medical and personal protective equipment (PPE).
Needle Punch Non-woven Fabric Machine: Needle punch machines are used to produce needle punch non-woven fabrics, which are made by mechanically interlocking fibers using barbed needles. Needle punch fabrics are strong and durable, and are commonly used in automotive and construction applications.
Thermal Bond Non-woven Fabric Machine: Thermal bond machines are used to produce thermal bond non-woven fabrics, which are made by bonding fibers together using heat. Thermal bond fabrics are commonly used in hygiene products, as well as in filtration and insulation applications.
Air-laid Non-woven Fabric Machine: Air-laid machines are used to produce air-laid non-woven fabrics, which are made by dispersing fibers in a stream of air and then bonding them together using heat or pressure. Air-laid fabrics are soft and absorbent, and are commonly used in hygiene and personal care products.
These are just a few examples of the many types of non-woven fabric machines produced in China. The specific type of machine used will depend on the desired properties and applications of the non-woven fabric being produced.
What are the advantages and disadvantages of using meltblown non-woven fabrics in PPE?
Meltblown non-woven fabrics have become an important component in the production of personal protective equipment (PPE), China non woven fabric machine especially for respiratory protection. Here are some advantages and disadvantages of using meltblown non-woven fabrics in PPE:
Advantages:
High filtration efficiency: Meltblown non-woven fabrics have a very fine fiber diameter, which allows them to capture small particles and aerosols. This makes them highly effective at filtering out airborne contaminants.
Low air resistance: Despite their high filtration efficiency, meltblown non-woven fabrics have a low air resistance, which means they allow for easy breathing and do not impede airflow.
Lightweight and comfortable: Meltblown non-woven fabrics are lightweight and soft, which makes them comfortable to wear for extended periods of time.
Cost-effective: Meltblown non-woven fabrics can be produced in high volumes and at a relatively low cost, which makes them an attractive option for manufacturers of PPE.
Disadvantages:
Limited durability: Meltblown non-woven fabrics are not as strong or durable as other types of materials, such as woven fabrics. This means they may need to be replaced more frequently, which can increase the overall cost of PPE.
Vulnerable to moisture: Meltblown non-woven fabrics can lose their filtration efficiency when exposed to moisture, which is a concern in humid environments or when PPE is used for extended periods of time.
Limited availability: The increased demand for PPE during the COVID-19 pandemic has led to a shortage of meltblown non-woven fabrics, which has made it difficult for some manufacturers to produce PPE.
Overall, meltblown non-woven fabrics offer many advantages for use in PPE, particularly for respiratory protection. However, there are also some limitations and challenges associated with their use that need to be taken into consideration.
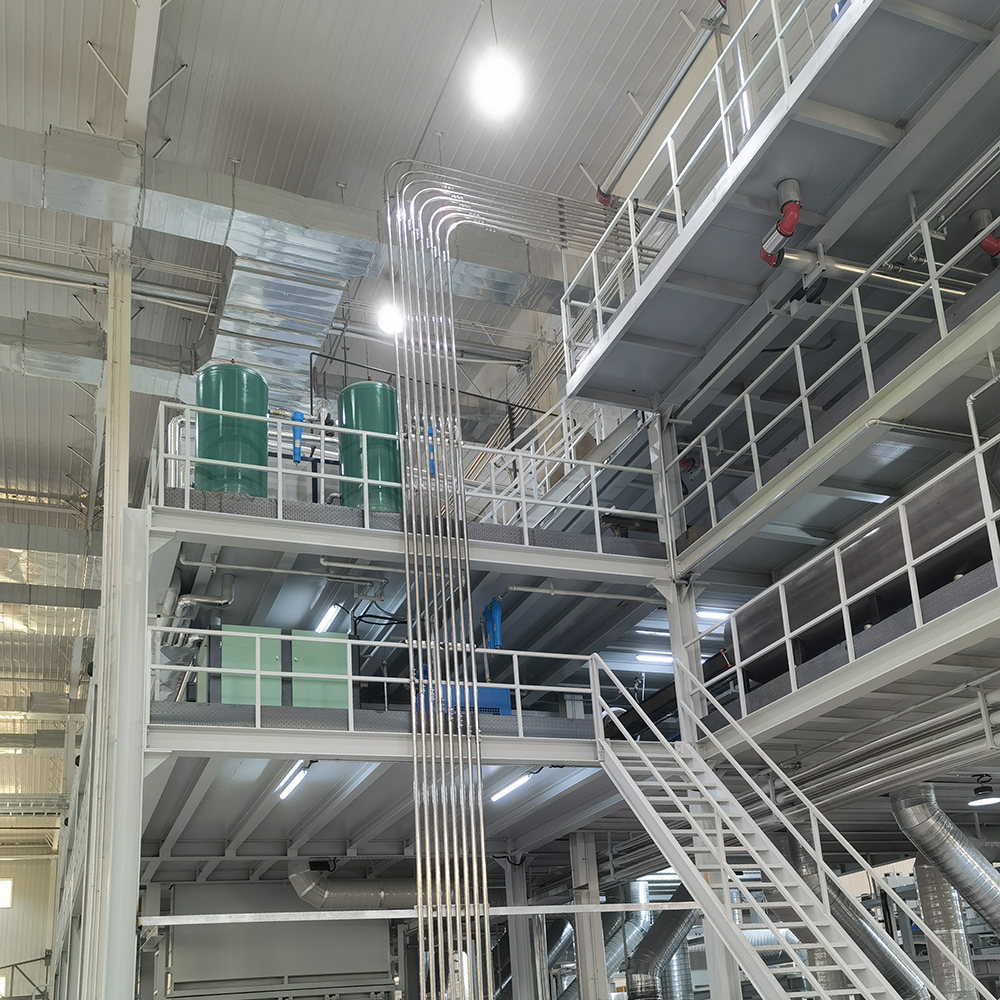