Installing an excavator undercarriage can be a complex process, and there are several common mistakes that you should avoid to ensure that the undercarriage is installed correctly and functions properly. Excavator undercarriage manufacturer advice some common mistakes to watch out for:
Incorrect tensioning
Failing to properly tension the tracks can result in premature wear and damage to the undercarriage components. Make sure to follow the manufacturer’s instructions for tensioning the tracks and use a tension gauge to ensure that the tension is within the recommended range.
Misalignment of components
Misalignment of undercarriage components can cause uneven wear and damage to the undercarriage. Make sure to check the alignment of the tracks, rollers, and sprockets during installation and adjust as necessary to ensure that they’re properly aligned.
Poor quality components
Using low-quality undercarriage components can lead to premature wear and failure of the undercarriage. Always use high-quality components from a reputable supplier to ensure that the undercarriage performs reliably and lasts as long as possible.
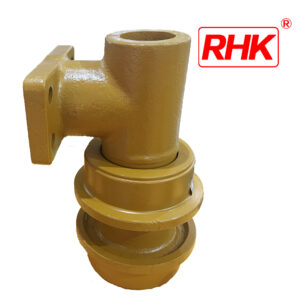
Incorrect installation sequence
Failing to follow the correct installation sequence can result in misaligned or damaged components. Always follow the manufacturer’s instructions for the correct installation sequence and make sure to torque all bolts and fasteners to the recommended specifications.
Incorrect lubrication
Failing to properly lubricate the undercarriage components can result in excessive wear and damage. Make sure to use the correct type and amount of lubricant and follow the manufacturer’s instructions for lubrication intervals.
By avoiding these common mistakes and following the manufacturer’s instructions carefully, you can ensure that your excavator undercarriage is installed correctly and functions properly for years to come.