Cast iron threaded fittings are known for their durability and longevity. When properly installed and maintained, they can have a lifespan of 50 years or more.
However, the actual lifespan of cast iron threaded fittings can vary depending on several factors:
Quality of the Fittings: The quality of the cast iron fittings is a key determinant of their lifespan. Higher-quality fittings manufactured to industry standards and specifications tend to have better longevity compared to lower-quality or substandard fittings. It is important to source fittings from reputable manufacturers or suppliers to ensure their quality and performance.
Installation: Proper installation is crucial for the longevity of cast iron threaded fittings. The fittings should be installed following the manufacturer’s guidelines and industry best practices. Adequate thread engagement, correct torque values, and the use of appropriate thread sealants or tape can ensure a secure and leak-free connection. Improper installation practices can lead to premature failure of the fittings.
Operating Conditions: The operating conditions to which the fittings are exposed can significantly impact their lifespan. Factors such as temperature variations, pressure fluctuations, exposure to corrosive substances, and mechanical stresses can affect the integrity of the fittings over time. It is important to consider the compatibility of the fittings with the specific operating conditions and make any necessary adjustments or use additional protective measures if required.
Maintenance and Inspections: Regular maintenance and inspections are essential for ensuring the longevity of cast iron threaded fittings. Periodic checks for leaks, signs of corrosion, and any visible damage or degradation can help identify issues early on. Prompt repairs or replacements of damaged or deteriorated fittings can extend their lifespan.
Environmental Factors: Environmental factors, including soil conditions, moisture levels, and the presence of corrosive substances, can impact the lifespan of cast iron threaded fittings. In corrosive environments, additional protective coatings or linings may be necessary to prevent or minimize corrosion. Proper soil conditions and adequate drainage can also contribute to the fittings’ longevity.
It’s important to note that the lifespan of cast iron threaded fittings can be influenced by the specific circumstances and conditions in which they are used. china hydraulic pump parts supplier Regular inspections, proactive maintenance, and adherence to operating guidelines can help maximize the lifespan of cast iron threaded fittings and ensure their optimal performance over time.
How often should hydraulic pump parts be inspected for wear and tear?
The frequency of inspections for hydraulic pump parts depends on several factors, including the specific application, operating conditions, and manufacturer recommendations. However, as a general guideline, hydraulic pump parts should be inspected for wear and tear at regular intervals to ensure optimal performance and reliability. Here are some considerations:
Manufacturer Recommendations: Follow the manufacturer’s guidelines and recommendations for inspection intervals. Manufacturers typically provide maintenance schedules and guidelines specific to their pump models. These recommendations consider factors such as operating hours, duty cycle, and environmental conditions.
Operating Conditions: Harsh or demanding operating conditions may require more frequent inspections. If the hydraulic pump operates in extreme temperatures, high pressures, contaminated environments, or experiences heavy loads or frequent cycles, more frequent inspections may be necessary.
Preventive Maintenance Program: Implementing a preventive maintenance program can help establish a regular inspection schedule. This program can include periodic inspections of hydraulic pump parts, along with other maintenance tasks such as fluid analysis, filter replacements, and system checks. The frequency of inspections can be determined based on the equipment’s criticality and the desired level of reliability.
Visual Inspections: Perform visual inspections regularly to check for visible signs of wear, leaks, or damage. Look for signs of fluid leakage, loose connections, worn seals, or excessive vibration. Inspect the pump housing, pistons, valves, and other components for any indications of wear, scoring, or corrosion.
Performance Monitoring: In addition to visual inspections, monitor the performance of the hydraulic system. Changes in system behavior, such as decreased flow rate, increased noise, or reduced efficiency, can indicate potential issues with the pump parts. Regularly monitor these performance parameters and investigate any deviations from normal operation.
Maintenance History: Consider the maintenance history of the hydraulic pump and its parts. If there have been previous instances of component failures or wear-related issues, it may be necessary to increase the frequency of inspections to proactively address potential problems.
Remember that regular inspections are essential for identifying wear and tear before it leads to major failures or system downtime. Timely detection of issues allows for planned maintenance or replacement of worn parts, minimizing the risk of unexpected breakdowns and reducing overall repair costs.
Consulting the pump manufacturer’s documentation, seeking guidance from hydraulic system experts, or partnering with maintenance professionals can help determine the appropriate inspection frequency for your specific hydraulic pump and application.
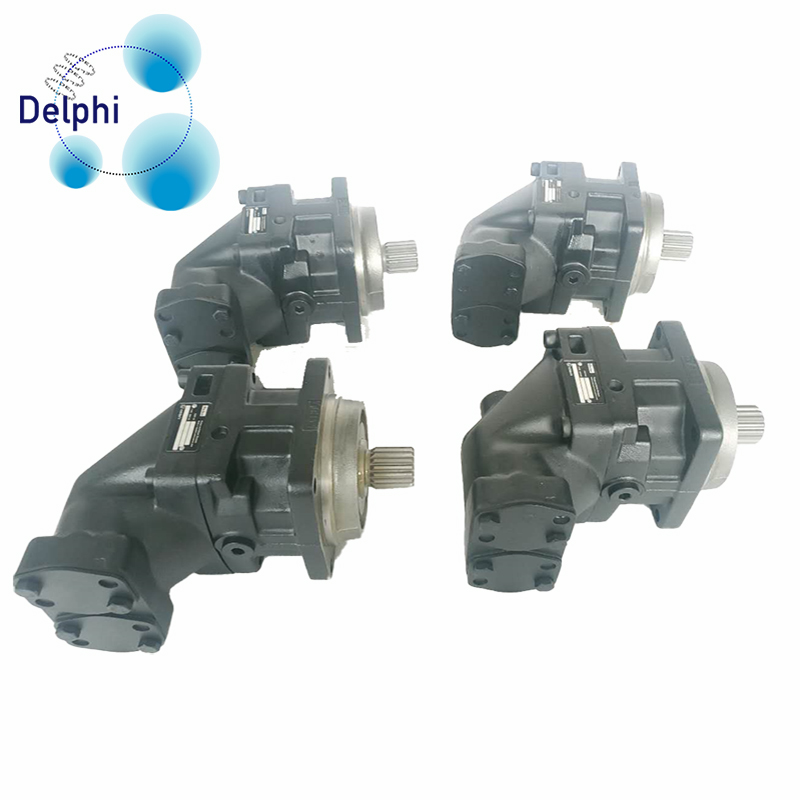